Hagg Press is a ‘Top 400 Printer’ according to Printing Impressions in the USA. The family company has been on this prestigious list for many years now. Established in 1975, Hagg Press is based in Elgin, Illinois and serves the thriving Chicagoland print market. Business is largely through resellers and is extremely competitive.
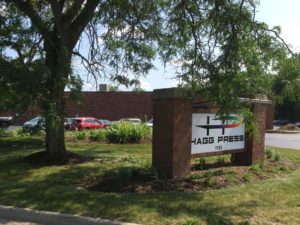
The management team at Hagg are strong believers in new technology. In the words of Jordan Hagg, Vice President of the company: “New technology is a requirement in this industry – you have to have it – if you don’t have it, you are definitely falling behind.” This pioneering approach led to their first installation of a GEW LED UV curing system in 2018, retrofitted to their RMGT 10-Series press.
The decision to install LED was largely driven by the press manufacturer, as Jordan explains: “After a lot of reading, a lot of talking to people, everything put together it really seemed to be LED UV as being the technology for the future. RMGT came to the table with a few options and GEW was very strongly suggested by them.” He goes on: “When we turned our LED system on for the first time and ran our first press sheet through there and we all stood at the console looking at this sheet and putting our fingers across it and realizing ‘this thing is dry… there’s no coating on it, it went right through the press, we just watched it.’ It was like magic and everybody looked at each other like… the game has changed at Hagg Press.”
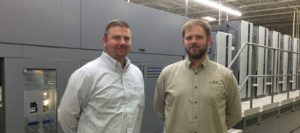
Brother to Jordan, Taylor Hagg is also a company VP. He focuses most of his time on production output, which has been transformed by the installation of LED UV. He explains: “The LED UV has definitely made my bindery work a lot easier because in the past with our conventional inks, we had a lot of issues with the inks not drying even days after a job was printed… and if the ink is still wet it tends to mark and scuff and you have problems in the post-press world. While with the curing of the LED inks, we are able to go right from press into our bindery equipment without issues at all. Everything about the job is easier post-press because you’re not also dealing with spray powder possibly causing issues down the line, of piling up on your other equipment, on rollers and feed mechanisms.”
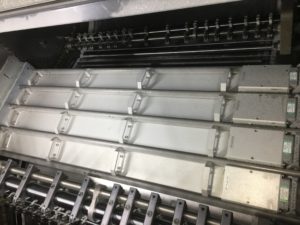
The press is installed with a GEW LeoLED Modular Lamp Array (MLA) system, which gives the print team a great deal of production flexibility, as Jordan Hagg clarifies: “Right now we have one lamp after the printing units and four lamps after the coating unit. With this arrangement we don’t have to move lamps and we can actually print any way we want – we can print four colour with no coating, we can print four colour with coating, we can print four colour with aqueous coating – and we can do everything in line without requiring two passes. With that we can achieve curing on any coating we want, at any speed we want.”
They also have the ability to control the lamp system individually, where they can cure after the fifth printing unit as well as after the coating unit. This means that they can achieve a dry trap of the coating by curing the inks before they reach the coater unit, which creates a glossier finish to the UV coating.
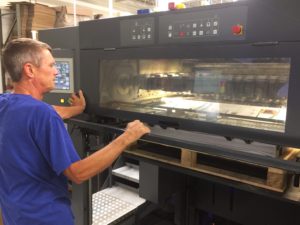
With the installation of the LED UV curing system, Hagg can now do the work of several presses with just the one RMGT 10 press. In the words of Jordan: “For the last 20 years Hagg Press had a perfecting press but when you go to print two sides you still have the dry time problem and with the LED UV I can print one side, flip the sheets over and put them right back through the press within five minutes – and I basically just achieved what our perfecting press had been doing for the last 20 years – all with a straight press. I’m able to pull work off of four presses and put it all on our LED UV 40-inch press, run it around the clock and I would argue outperform all other presses combined with one-shift operation.”
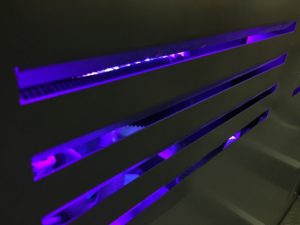
On the question of the return on investment period for the LED UV system, Jordan comments: “With LED we do not need to use the IR dryers that we did need with conventional inks… because of that we’re saving money on electricity, with regard to not just the power output of the IR dryers versus the LED, but also the heat output – the IR dryers put out a lot more heat and because of that our air-conditioning in the summertime was huge – the bills were giant – now they’re much lower. I would venture to say they are a couple of thousand dollars a month cheaper. It’s not going to be very long before this system pays for itself.”
Taylor Hagg concludes: “With LED our turnarounds are much faster, our quality is certainly above where it used to be, it’s worked perfectly flawless the entire time and we just can’t wait to get the next one.”
###
To find out more about how GEW meets the needs of Sheetfed Offset customers, visit our Sheetfed Offset page.
Visit our LeoLED2 page to find out more about our latest UV LED product for Sheetfed Offset, or watch the case study video below:
###